
Architects: design/buildLAB at VA Tech School of Architecture + Design
Location: Clifton Forge, Virginia
Project Team: Tyler Atkins, Lauren Duda, Huy Duong, Derek Ellison, Megumi Ezure, Katherine Harpst, Kyle Lee, Leo Naegele, Margaret Nelson, Leah Schaffer, Ian Shelton, Brent Sikora, Emarie Skelton, Samantha Stephenson, Taylor Terrill, Samantha Yeh (All students of VA Tech). Along with Marie Zawistowski, Architecte DPLG (Professor of Practice); Keith Zawistowski, Assoc. AIA, GC (Professor of Practice).
Year: 2011 – 2012
Photographs: Jeff Goldberg/ESTO
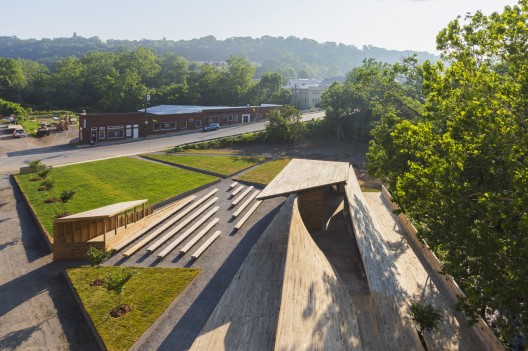
Project Description:
The project consists of the complete redevelopment of a post-industrial brownfield into a public park and performance space. The idea driving the design is that the built elements are sculptural forms emerging out of the landscape of the park. The park is a series of extruded lawns and carved paths that knit the surrounding urban fabric into the site’s circulation. The built elements include a stage with acoustic shell, a backstage with loading dock, green room and wings, a seating area, and a sound and lighting control booth.
The ground plane is peeled up from the stage to create its shell. Steam-bent white oak walls curve to define secluded pockets offstage and intermediary zones of varying intimacy, allowing performers to slip in and out of audience view. The interior walls and ceiling of the shell are sculpted to naturally project acoustics toward the audience.
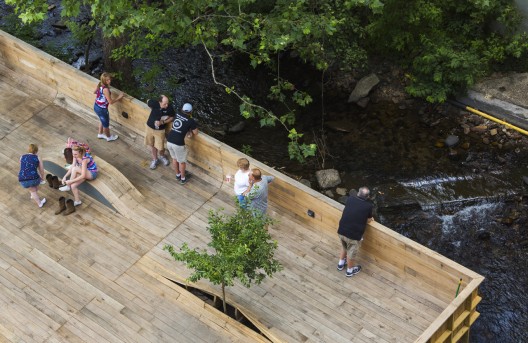
Its interior is lined in CNC-routed composite panels with aluminum, zinc, titanium and stainless steel skins. The backstage area is conceived as a creek-side terrace: an intimate place for waiting performers or a casual place for social interaction. To this end, benches pull up from the deck to invite pause and crape myrtle trees push through its surface to provide shade. The rough-sawn white oak cladding dampens the noise of the rushing creek water, allowing it to resonate on the backstage terrace but muting it from the stage and audience.
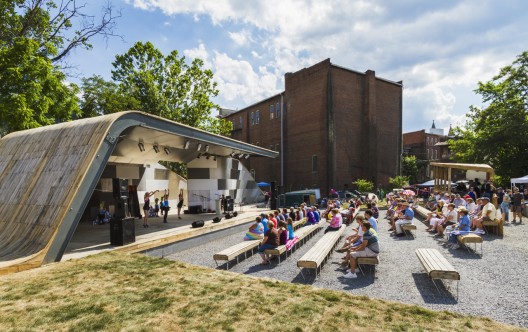
Wood benches provide cool summer seating for an audience of 200 in the sloping gravel orchestra. Staggered alignment allows for wheel chairs and folding chairs to be dispersed within the audience rather than at the periphery. A central aisle, sliced diagonally through the benches, allows people to get in and out with minimal disturbance to their neighbors and accentuates a major pedestrian axis across the town. The elevated lawns provide overflow seating for an additional 800. Sound and lighting is controlled from a covered booth: an oak wedge, nested at the corner of the seating area. Its shape and location provide maximum shelter for the control equipment with minimal impact on audience sight lines. The material pallet anchors the project in its context, while the timeless contours reflect the creativity and aspirations of a forward thinking community.
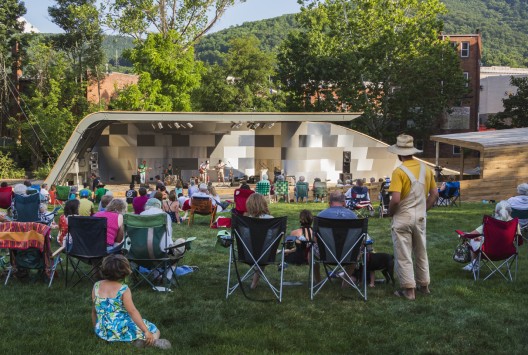
Urban Revitalization:
Clifton Forge, Virginia is representative of many previously prosperous American rail towns, struggling to survive as the industries, which fueled their growth, continue to abandon them. Tucked within a small valley along the Jackson River, this rural Appalachian town faces severe urban challenges. Deserted storefronts, empty houses, and decaying infrastructure all contribute to an underlying sense of abandonment.
The redeveloped site provides much needed public space along the creek, at the center of town. The park and amphitheatre serve to knit together the fragments of a fledgling arts based re-vitalization in neighboring buildings. The Masonic Amphitheatre is a cultural anchor that belongs to the community at large. It is a vibrant center of spontaneous public gathering that promotes community, supports local businesses, and nurtures the arts.
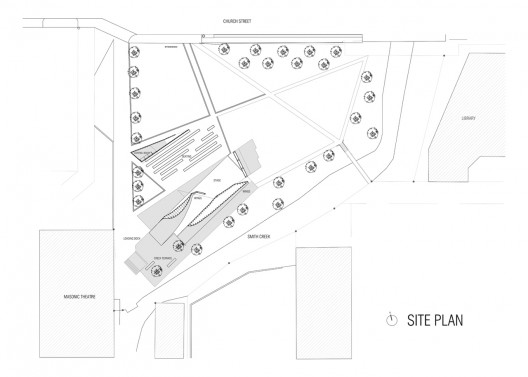
Collaboration:
The Masonic Amphitheatre is a charitable undertaking that was designed and built by 16 third year undergraduate Architecture students from Virginia Tech’s design/buildLAB. After studying the town and working with the community to develop a program, all 16 students made individual design propositions for the project. From those, a master plan was determined, and students iteratively merged their proposals. In this way, all of the students contributed ideas to the discussion. It was imperative from a pedagogical perspective that not one “scheme” was chosen. Rather, all students collaborated to develop the final design for the project.
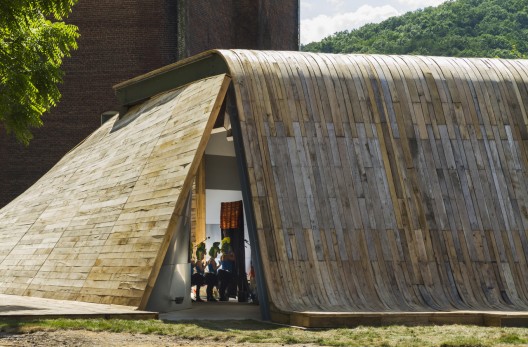
Sustainability:
Material re-use was essential to the project’s sustainable approach. To this end, the decaying industrial warehouse that previously occupied the site was disassembled rather than demolished. The vast majority of its material, including pine timbers and galvanized cladding, were re-purposed to build a Farmers Market in a neighboring town. Materials like scrap metal and plastics, not suitable for re-use, were re-cycled.
Because the site previously housed an industrial production facility, its warehouse sat on a massive concrete plinth that was conserved as the stage and foundation for the new amphitheatre, minimizing concrete use and disturbance along the adjacent creek.
All new surfaces are pervious, minimizing run-off to the delicate creek ecosystem. To this end, new floors are wood decking and new hard surfaces are compacted gravel fines. Lumber, including white oak decking, was sourced from locally sawn timbers. LED lighting ensures long bulb life and extremely low energy consumption. Finally, the pavilion was oriented and shade trees were planted to limit solar gain and eliminate the need for mechanical cooling.
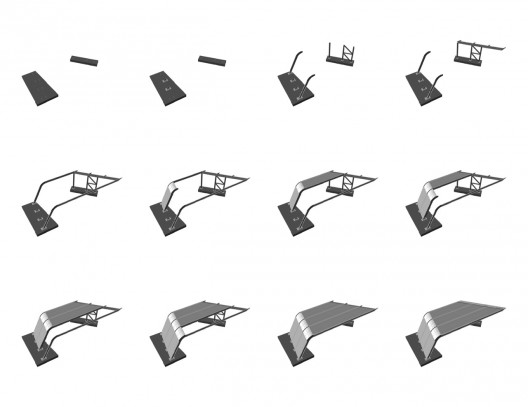
Digital Fabrication:
Digital fabrication played a substantial role in the sustainability of the project by maximizing structural efficiency and minimizing waste. The structure of band shell walls are comprised of prefabricated wood trusses. The geometry of the trusses was determined by cutting the 3D model every two feet on center. The trusses were then machine fabricated offsite by a conventional wood truss manufacturer. This helped to minimize waste and time spent manufacturing.
Additionally, the Alpolic Metal Composite panels used to clad the underside of the band shell were digitally fabricated. Due to the curved nature of the building, the size and shape of each panel was different. In order to ease the process, each panel’s size and shape was determined using a 3D model then cut using Virginia Tech’s CNC router.
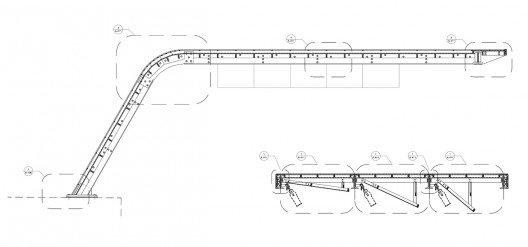
Prefabrication:
All component parts are based on a 10’ wide module to facilitate prefabrication and transportation to the site. At the scale of the town, the building reads as a seamless gesture. At the scale of the occupant, the details express the modular construction.
The students prefabricated the Amphitheatre structure, including floor, walls, sound booth, roof panels, and benches at VA Tech’s Environmental Systems Laboratory. A local contractor was hired to complete the foundations and utility connections. This allowed for two phases of construction, site work and framing, to happen simultaneously. In total, the students prefabricated and assembled the structure in less than four months. The efficiency of working in a controlled environment, with easy access to tools and equipment was essential in achieving the schedule of one academic year.
Masonic Amphitheater Time-Lapse by Jeff Goldberg/Esto:
Owner: Masonic Amphitheatre LLC
General Contractor: Commonwealth Contracting Services
Structural/Civil Engineer: Draper Aden and Associates
Theatre Consultant: Theatre Consultants Collaborative
Acoustical Consultants: Michael Ermann, Ana Jaramillo
Environmental Impact Consultant: Robert Schuber
Geotechnical Engineer: Froehling & Robertson, Inc
Hydraulic Engineer: Hassan Water Resources
Truss Engineering: Timber Truss
CAM Technician: Chip Clark
Landscape Consultant: Brian Katen Owner
Project Funding: $150,000 cash grant from The Alleghany Foundation and significant in-kind material and service contributions from local contractors and suppliers, as well as national and international product manufacturers.
Materials: Alpolic Metal Composite Panels: Mitsubishi Plastics Composites, White Oak Decking: Union Church Millworks, Structural Steel: BMG Metals, Elastomeric Roofing: Hydro Stop, Prefabricated Wood Trusses: Timber Truss, Paint: Sherwin Williams, Conduits: Kelly Bev-Way, Concrete and Reinforcing Steel: Conmat Group, Electrical Components: State Electric, LED Lighting: RAB, Fasteners: Stafford Nut & Bolt, Sod: Lavery Sod Farm, Trees: Cooke’s Gardens, Heavy Equipment: United Rentals
Software: Rhino3D OSX, AutoCAD 2012 Mac (Educational Verison), CATT-Acoustic v9
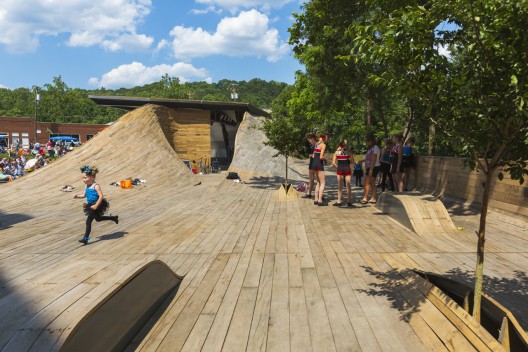




